A Comprehensive Guide to Getting Stuff Out of the Ground
Dig into the brown or greenfield of above ground mining access equipment with this comprehensive guide, which uncovers its essential role within the mining industry.
Whether you’re a mining expert, an industry enthusiast, or simply curious about this critical aspect of mining operations, this guide is your top resource for valuable insights and practical advice.
Definition and Overview of Above Ground Mining Access Equipment
Above ground mining access equipment refers to a wide range of machinery and tools specifically designed to facilitate access to various areas of a mining site. These equipment are essential for creating safe and efficient access routes for personnel, vehicles, and materials, enabling seamless operations across the mining site.
From access platforms to advanced extraction technologies, the scope of above ground mining access equipment is diverse and integral to the overall mining process.
SafeSmart Access’ Role in Above Ground Mining
SafeSmart Access has established itself as the leading supplier of height access solutions for the mining industry. With a focus on engineering custom solutions that prioritise safety and compliance, SafeSmart Access has responded to the ever-increasing demand for reliable and adaptable access equipment in mining.
You can read more about SafeSmart’s involvement with mines in their case studies:
-
Increasing Scaffold Safety for Mine Site, Mt Authur Coal, BHP
-
Ensuring Safety Across Trenches: Sedgman Limited’s Success
-
Hunter Valley supercharges safety and efficiency with SafeSmart solutions
-
BlueScope Train Maintenance Gets Elevated Safety at the Port
For a complete list of access solutions, visit our Above Ground Mining Solutions page for products and examples of mine safety success. Visit our Mining overview page for a quick snapshot of who we’ve worked with and our solutions.
Types of Above Ground Mining Access Equipment
Above-ground mining requires a variety of access equipment, each tailored to meet specific demands within the mining environment. Here’s a closer look at some key types of equipment used for site preparation and ground maintenance.
Site Preparation and Ground Maintenance
After a lease is granted, the site must be prepared for additional infrastructure to be built, often involving the removal of top soil and overburden to prepare for extraction. Once underway, roadways and access points need to be maintained around the opencast mine.
Mining Scraper
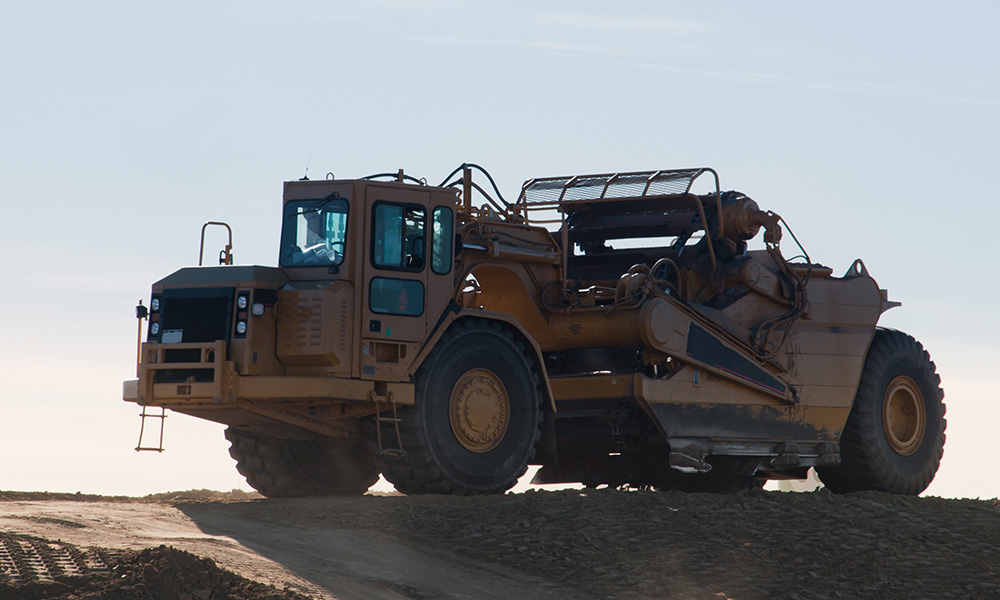
Scrapers are essential in site preparation for mining, designed to efficiently clear and level large areas, creating stable, accessible surfaces for operations. These machines cut, collect, and transport soil and debris in one smooth motion, streamlining the preparation process. With their high capacity and precision, scrapers reduce manual workload and expedite site readiness, ensuring a solid foundation for subsequent mining activities.
Grader Mining Equipment
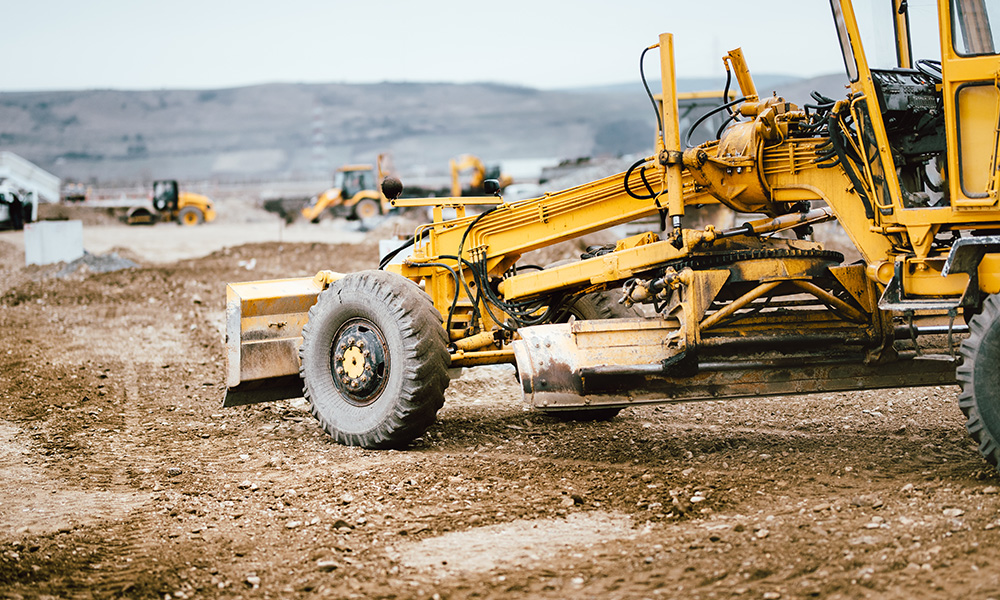
Graders are used to create level surfaces throughout the mining site, ensuring smooth and even access roads for vehicles and machinery. Equipped with an adjustable, long blade, these machines are essential for shaping access routes to the required level of flatness. Graders play a vital role in preparing the site, enhancing both safety and accessibility for ongoing mining operations.
Mining Dozer
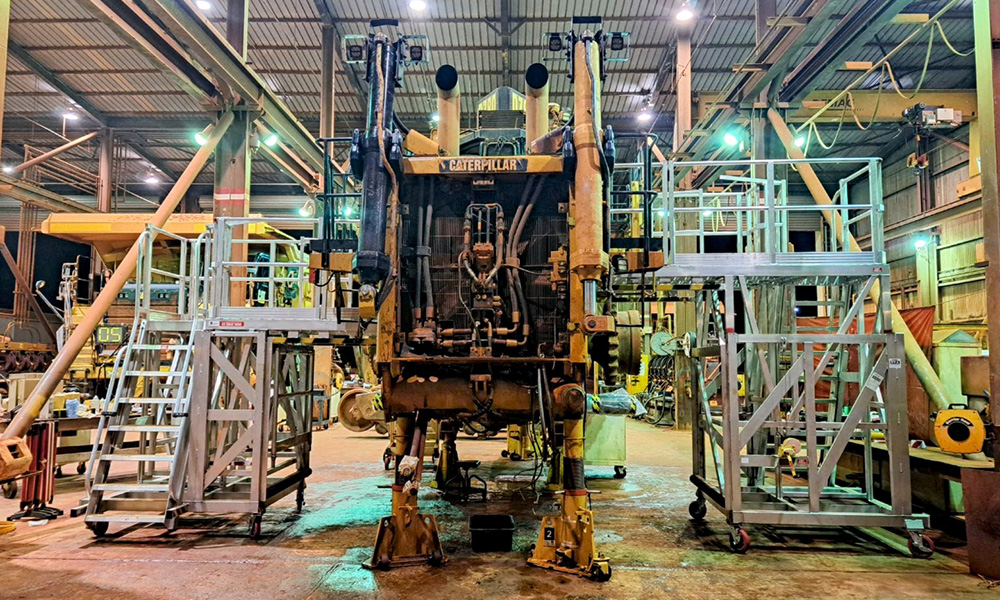
Mining dozers are robust, heavy-duty machines built to push and move large volumes of materials. They are essential for clearing, grading, and leveling access paths across the mining site. With their sturdy construction and powerful engines, dozers can handle rugged terrain, establishing reliable access routes even in challenging environments. Their versatility and strength make them indispensable for preparing the ground and maintaining accessibility throughout the mining site.
Both of these vehicles require frequent maintenance and can be difficult to move around various parts like air filter access. At times dozer platforms and grader platforms can help with this access.
Overburden & Material Excavation Vehicles
Efficient overburden and material removal are vital for preparing and maintaining access within above-ground mining sites. Here’s an overview of the primary excavation vehicles used in these operations.
Bucket Wheel Excavator
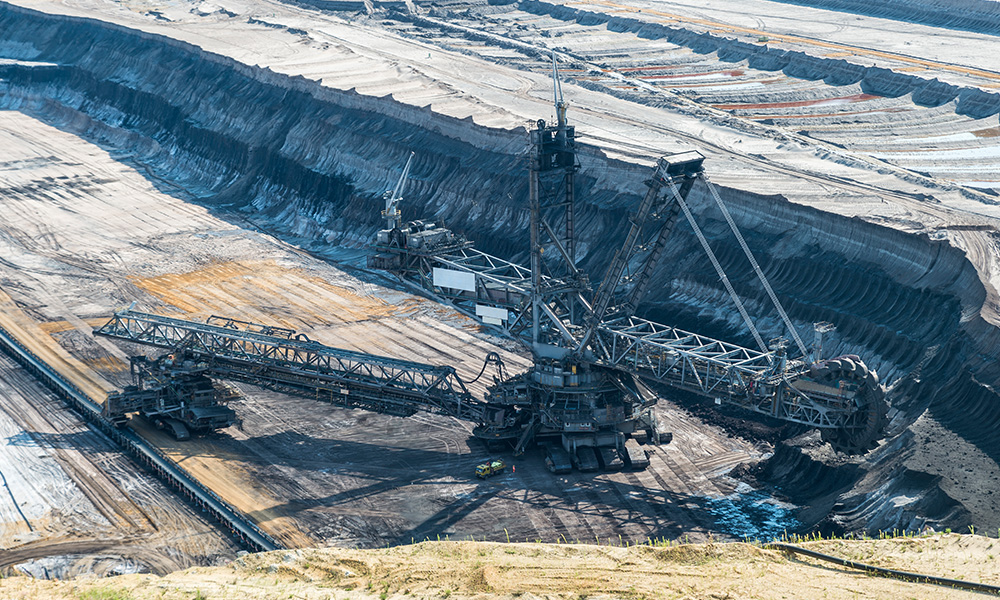
Bucket wheel excavators are enormous machines equipped with a rotating wheel fitted with multiple buckets, allowing for efficient excavation and transportation of large volumes of materials. In mining, they are primarily used to create access points and remove overburden—layers of soil and rock covering the valuable minerals—thus facilitating the extraction process.
Bucket Chain Excavator
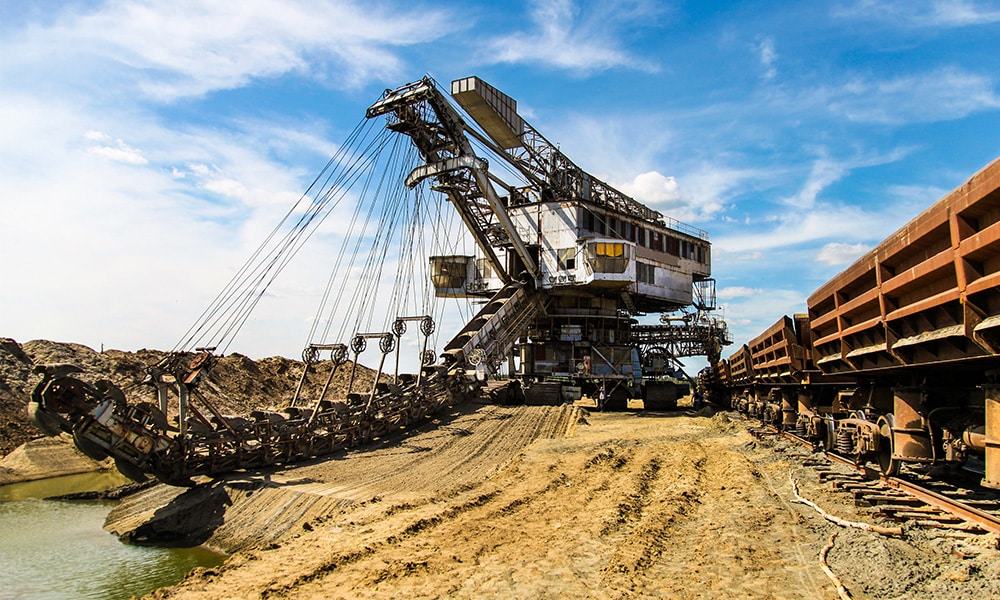
Similar in function to bucket wheel excavators, bucket chain excavators are built for extensive material excavation in mining environments. The continuous chain of buckets allows them to efficiently remove and transport significant quantities of material, making them essential for creating access paths and clearing targeted areas within the mining site.
Surface Miners
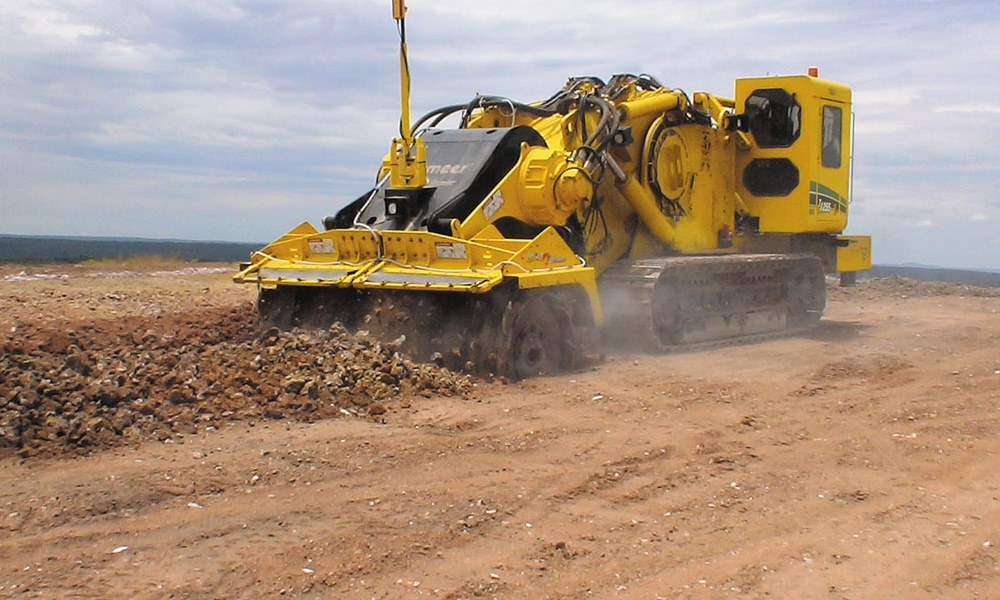
Surface miners are advanced, precision-driven machines designed for selective extraction of valuable minerals and materials from the site’s surface. By providing accurate and controlled excavation, surface miners contribute to the formation of access routes while minimising environmental impact through reduced waste and lower operational footprints.
Dragline Excavators
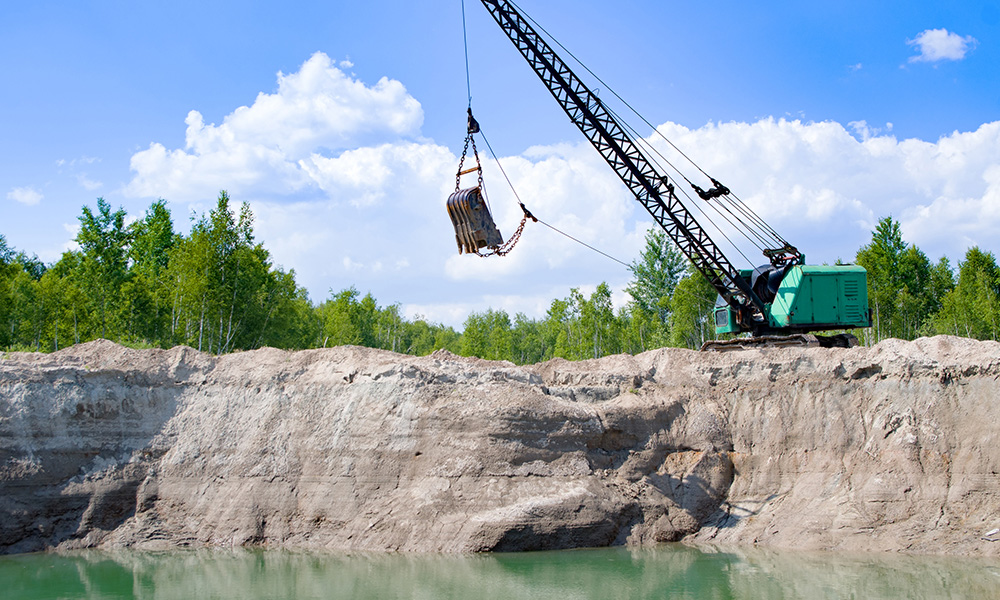
Dragline excavators are colossal machines equipped with a large bucket suspended from a long boom, making them suitable for extensive excavation and material handling tasks. Their capabilities in lifting and removing large amounts of overburden make them essential for creating access points and managing overburden in large-scale mining operations.
Mining Shovels
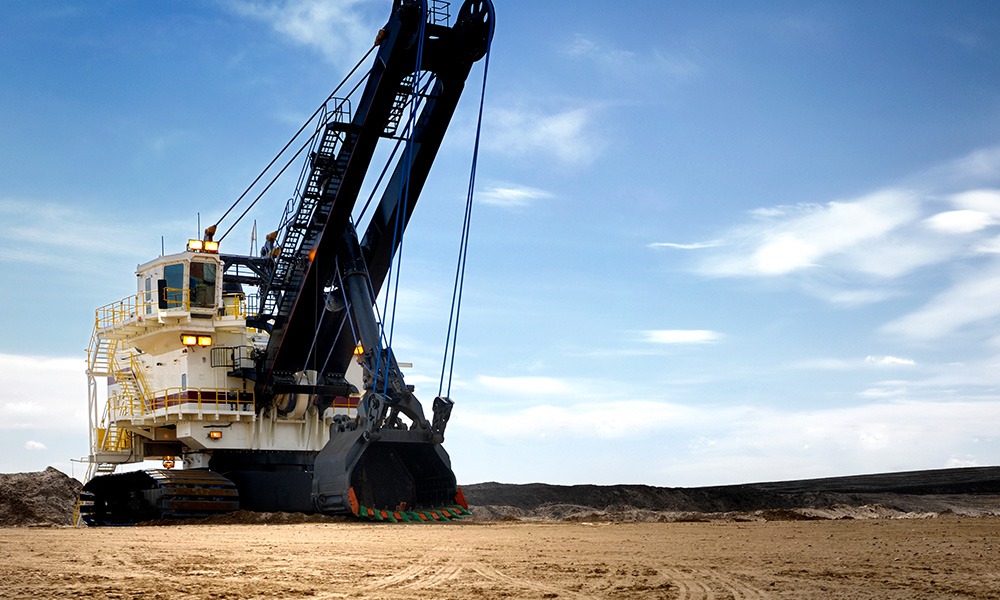
Mining shovels are powerful excavation machines designed with large buckets for handling substantial amounts of material. They are crucial for creating access paths, clearing debris, and removing overburden from the mining site, thus contributing to operational efficiency and smoother site accessibility.
Digging Excavators
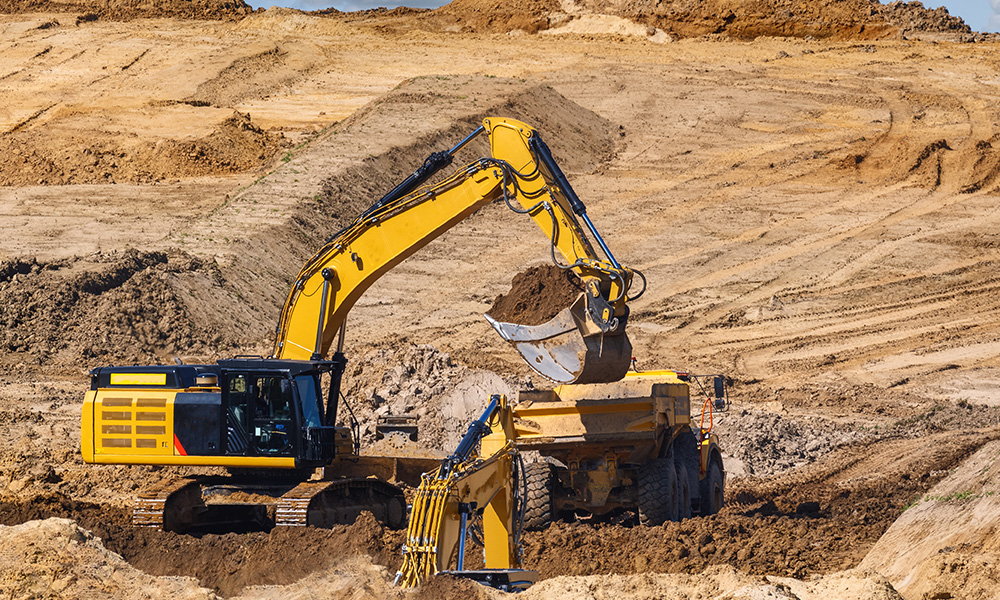
Digging excavators are versatile machines engineered to tackle a variety of excavation tasks, from creating access paths to removing obstacles and debris within the mining site. Their adaptability and precision make them invaluable for maintaining clear, efficient access routes throughout the mining area.
Loading, Hauling Dumping
Loading, hauling, and dumping are integral activities in above-ground mining, involving specialised machinery and skilled operators to ensure efficient transport and accessibility across the site.
Loaders
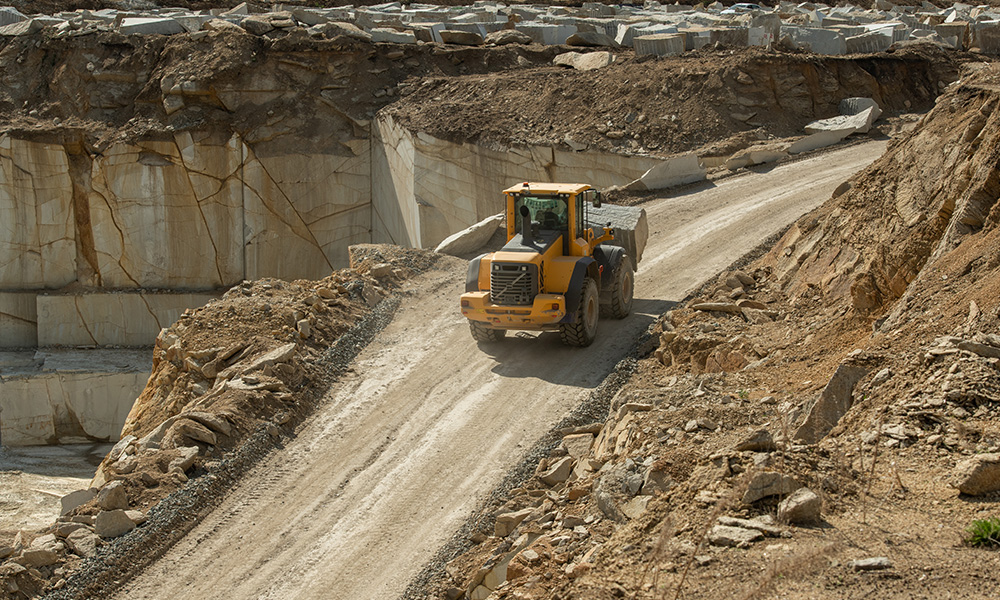
Loaders are powerful machines used for lifting and loading materials onto haul trucks and other transport vehicles. Their high-capacity buckets allow for swift material handling, contributing to the smooth and efficient loading process that supports site productivity and helps maintain access routes by efficiently moving debris and minerals as required.
Mining Haul Truck
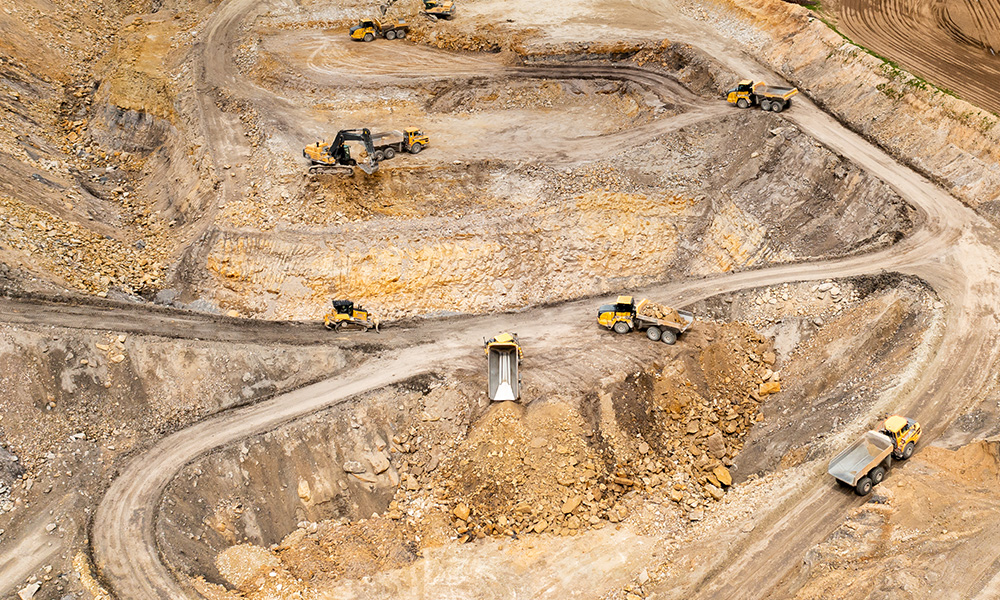
Mining haul trucks are heavy-duty vehicles engineered to transport large volumes of materials within the mining site, including overburden and valuable minerals. Built for durability and substantial load capacity, these trucks play a crucial role in supporting the creation and upkeep of access routes, ensuring materials are efficiently moved across the site to maintain a seamless workflow.
Articulated Haul Truck
Articulated haul trucks are highly versatile vehicles featuring a pivoting joint, allowing them to easily navigate rough or uneven terrains. Their adaptability and load capacity make them particularly valuable for transporting materials through challenging areas, creating efficient access routes and ensuring materials reach their intended destinations.
Haul Truck Operator
Haul truck operators play a critical role in managing the transportation of materials within the mining site, ensuring the creation and maintenance of efficient access routes. Their expertise and operational skills contribute to the overall productivity and safety of mining operations. For certain mines, these roles are done autonomously or via remote control.
Workshop Access Solution: UltraRaise
SafeSmart Access has introduced the UltraRaise platform, a height-adjustable work platform designed to enhance safety and efficiency in mining operations. This platform addresses common challenges in maintaining heavy mining vehicles, such as the Caterpillar 777 haul trucks.
- Height Adjustability: The platform can be adjusted to various heights, accommodating different maintenance tasks and vehicle sizes.
- Compact and Mobile Design: Its design allows for easy movement and deployment within tight spaces, facilitating access to hard-to-reach areas.
- Enhanced Safety: By providing stable and secure access, the UltraRaise platform reduces the risk of falls and injuries during maintenance activities.
The adoption of the UltraRaise platform by mining operators has led to improvements in maintenance turnaround times and a reduction in vehicle downtime, contributing to increased productivity and operational efficiency.
Bulk Material Handling Equipment
Bulk material handling is essential in mining, involving the controlled movement of large volumes of materials across the site. This requires specialised equipment and systems that ensure reliable access and efficient logistics throughout the mining environment.
Belt Wagons
Belt wagons are specialised vehicles fitted with conveyor belts, enabling them to transport materials efficiently and establish temporary access routes on the site. Their mobility and handling capabilities make them instrumental in optimising logistics and access within mining operations.
Crawler-Mounted Spreaders
Crawler-mounted spreaders are versatile machines designed to distribute materials such as overburden and waste rock across the mining site. By creating even and controlled layers of materials, these spreaders contribute to the maintenance of access routes and the overall organisation of the mining site.
Overland Conveyor
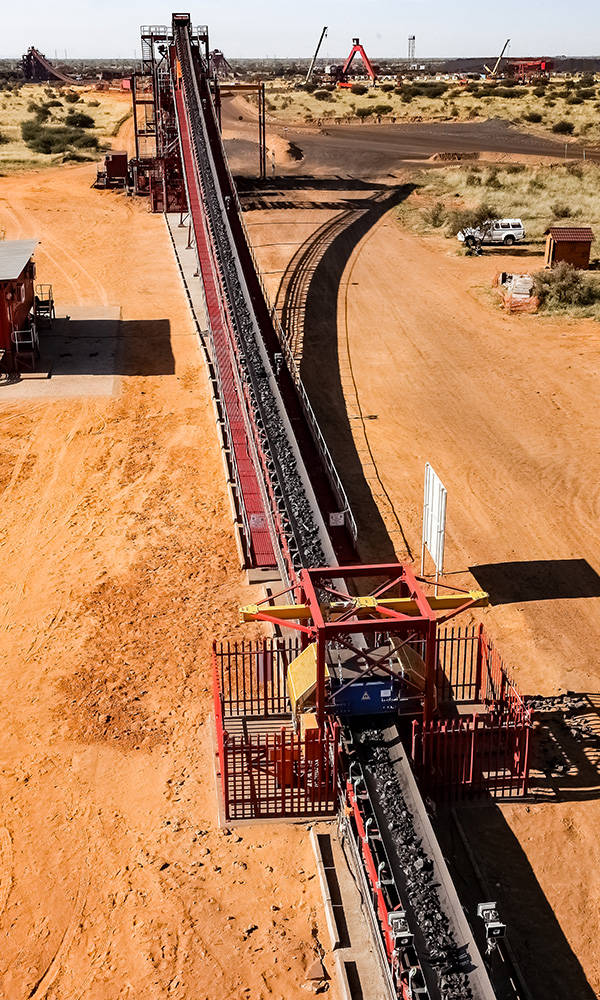
Overland conveyors are long-distance belt conveyors used to transport bulk materials over varied terrain. These conveyors play a critical role in creating efficient access routes for materials, enabling seamless transportation across the mining site.
Conveyor Belt Feed Trough
Conveyor belt feed troughs are components of conveyor systems designed to support and guide the conveyor belt, ensuring smooth and reliable material transportation. These troughs contribute to the creation of stable and efficient access routes for materials within the mining site.
Apron Feeder
Apron feeders are robust machines used to extract and feed materials in various mining applications. Their ability to handle heavy-duty materials makes them essential for creating reliable access routes and managing the flow of materials within the mining site.
Pipe Conveyor
Pipe conveyors are specialised conveyor systems that utilise enclosed belts to transport materials, offering advantages in terms of environmental protection and material containment. Their role in creating efficient and controlled access routes contributes to the overall safety and productivity of mining operations.
Conveying System Manufacturers
Conveying system manufacturers are crucial in providing innovative and reliable solutions for material transportation within the mining industry. Their expertise and technological advancements contribute to the development of efficient access equipment for mining operations.
Bucket Elevators
Bucket elevators are vertical conveyors designed to transport materials in bulk, utilising buckets attached to a rotating belt or chain. Their ability to handle various types of materials makes them valuable for creating vertical access routes within the mining site.
Conveyor Bridge
Conveyor bridges are structures that support conveyor systems, providing elevated access routes for material transportation across the mining site. Their design and construction contribute to the efficient movement of materials and resources within the mining environment.
Case Study: Conveyor Bridge Edge Protection
Yancoal partnered with SafeSmart Access to improve conveyor bridge safety, replacing inadequate edge protection with a customised guardrail system. The solution, featuring a modular design and durable materials, met stringent safety standards and integrated smoothly with existing infrastructure. Post-installation, Yancoal saw significant safety improvements, reducing fall risks and enhancing overall site protection with minimal operational disruption.
Crushers
In mining operations, crushers are essential for breaking down materials into manageable sizes, aiding in material handling and extraction processes. Various types of crushers are used depending on the specific needs and conditions of the site.
Cone Crushers, Jaw Crushers, and Impact Crushers
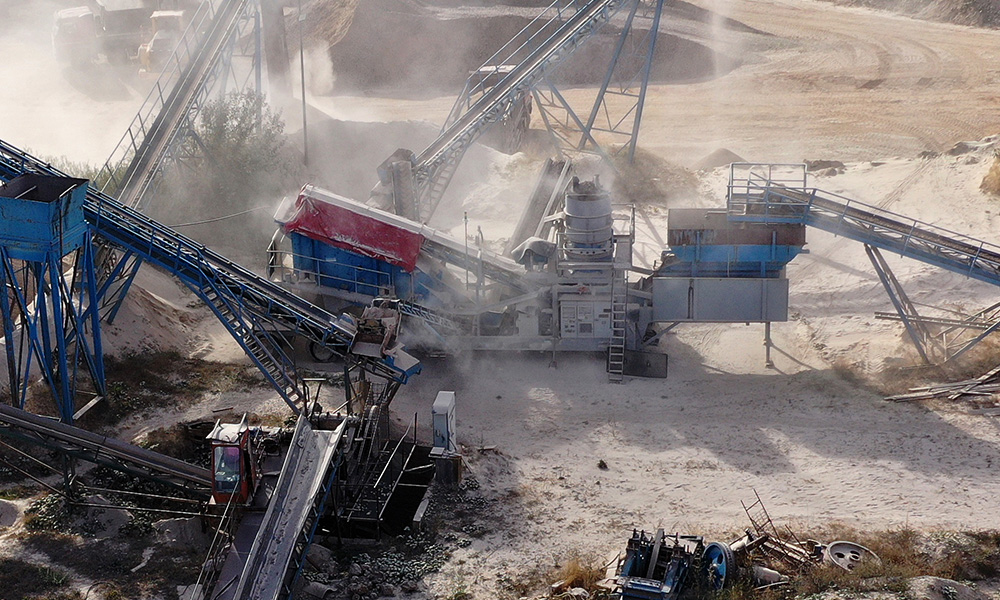
These are the most common types of crushers found in mining:
- Cone Crushers: Cone crushers use a rotating cone inside a hardened shell to break down materials, ideal for secondary crushing.
- Jaw Crushers: These crushers use a compressive force to crush large materials into smaller, more workable sizes, typically used for primary crushing.
- Impact Crushers: Impact crushers break down materials by using high-speed impact, making them effective for materials with lower abrasiveness.
Each type serves a unique purpose, contributing to efficient material reduction within the mining site.
Gyratory Crushers
Gyratory crushers are robust, heavy-duty machines designed for high-capacity primary crushing. Using a gyrating spindle to apply compressive force, these crushers are suitable for handling large amounts of hard material, making them valuable for initial material reduction in extensive mining operations.
Rollers and Sizers
Rollers and sizers are crushers designed for softer, less abrasive materials.
- Roller Crushers: Roller crushers use two cylindrical rollers to crush materials into finer sizes, useful for handling materials like coal.
- Sizers: Sizers are designed to crush and size soft materials through compression and shearing, offering effective handling of materials with consistent particle size distribution.
Mobile and Portable Crushers
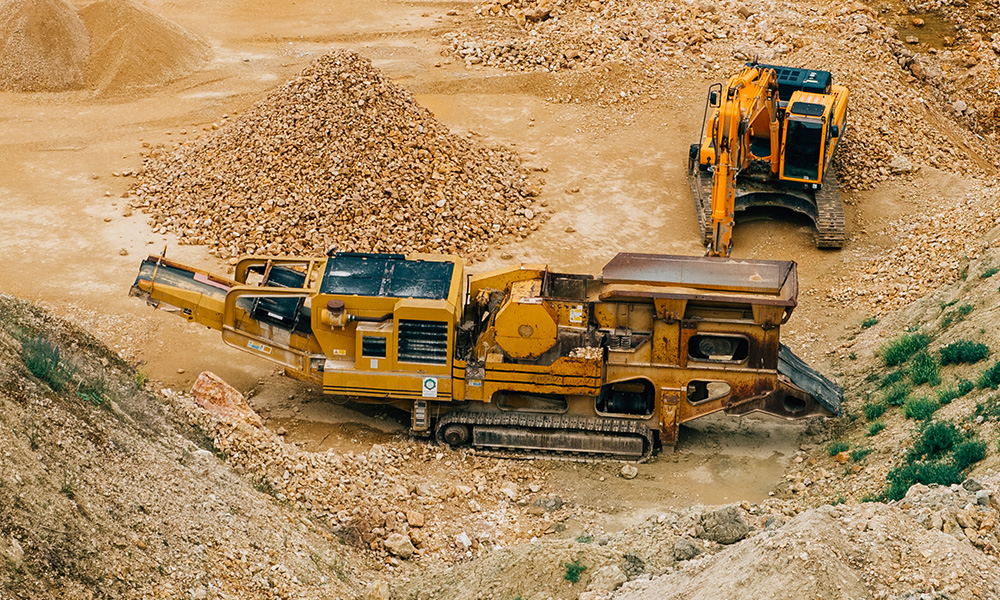
Mobile and portable crushers provide flexible, on-site crushing solutions. These units can be relocated across the mining site, allowing for on-demand crushing closer to excavation areas. Their mobility reduces material transport costs and supports efficient site operations.
Electric Crushing and Screening Solutions
Electric crushing and screening solutions are powered by electric motors rather than traditional diesel engines, offering reduced emissions and lower operational costs. These eco-friendly crushers are particularly valuable in environmentally conscious operations, supporting sustainability while ensuring efficient material processing.
In-Pit Crushing System
In-pit crushing systems are comprehensive solutions combining crushers and conveyors to manage material handling directly within the mining site. By reducing the need for traditional truck haulage, these systems play a critical role in enhancing site efficiency, creating access routes, and streamlining material transportation for processing.
In-Pit Crushing and Conveying
In-pit crushing and conveying (IPCC) systems integrate crushers and conveyor systems to handle materials within the mining area. By locating crushing and conveying systems closer to the extraction points, these setups reduce truck usage, lower operational costs, and minimise environmental impact. IPCC systems enable the continuous, efficient movement of materials, supporting accessibility and optimising the flow of resources across the site.
In-Pit Crushing Plants
In-pit crushing plants are either stationary or mobile facilities that incorporate crushers and conveyors for on-site material processing. Positioned at the extraction site, these plants streamline operations by allowing immediate processing of extracted materials. In-pit crushing plants help to minimise material transportation distances, contributing to greater operational efficiency and facilitating accessible, on-site processing within the mining area.
Breakers
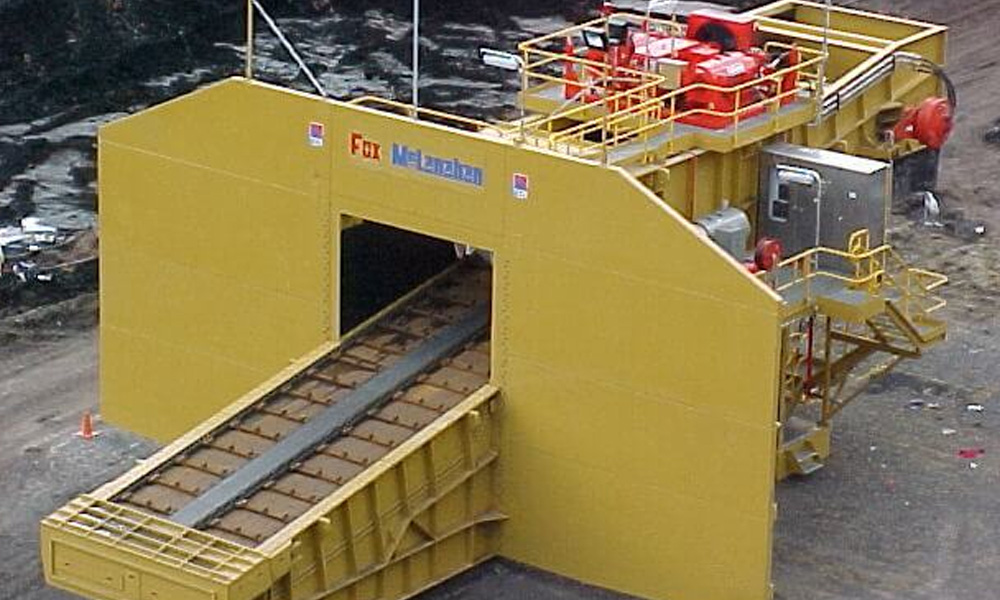
Breakers and mills are essential in mining operations, designed for crushing, grinding, and preparing materials for further processing. These machines play a significant role in the initial stages of material handling, ensuring efficient breakdown and feedfeeding into subsequent processes.
- Rock Breakers: Rock breakers are large hydraulic machines used to break down oversized rocks and boulders. Typically positioned near crushers, they allow for easier handling and processing by reducing the size of large materials before they enter crushers or conveyors.
- Feeder-Breakers and Reclaim Feeders: Feeder-breakers are used to crush and feed bulk materials from a high-capacity hopper into the processing stream, maintaining a consistent material flow. Reclaim feeders perform a similar function by recovering stored materials and feeding them back into the system, ensuring seamless operation and continuous material availability.
Mining Screens
Mining screens are specialised equipment used to separate and classify materials based on size and composition. Their role in the mining process contributes to the efficient management of materials and the creation of access routes for specific types of materials.
Vibrating Screens
Vibrating screens use rapid oscillations to sort materials by size, with different sections of the screen allowing specific particle sizes to pass through while larger pieces remain on top. These screens are highly effective for sifting large volumes of material, ensuring that only correctly sized materials proceed to the next stage of processing. Vibrating screens are widely used in mining for their reliability and capacity to handle heavy-duty materials.
Scalpers
Scalpers are a type of vibrating screen designed to remove oversized material from the mining stream early in the process. Positioned at the start of the material flow, scalpers help prevent large, unwanted materials from entering further processing stages, protecting equipment from wear and ensuring only correctly sized materials move forward. They play a crucial role in managing the material flow and maintaining the efficiency of subsequent screening and crushing equipment.
Banana Screens
Banana screens are high-capacity vibrating screens with a curved, multi-slope design resembling the shape of a banana. This unique shape allows them to handle large volumes of material, providing efficient classification and separation. Ideal for applications requiring high throughput, banana screens are instrumental in managing material flow, contributing to organised and accessible routes within the mining site.
Horizontal Screens
Horizontal screens are versatile vibrating screens that operate parallel to the ground, offering stable and efficient classification of various materials. Their adaptability makes them valuable across a range of mining processes, ensuring smooth material handling and supporting the creation of organised and efficient access routes throughout the site.
Inclined Screens
Inclined screens are vibrating screens positioned at an angle, which helps materials move more effectively across the screen. The incline increases the screen’s throughput capacity, making it suitable for sorting and classifying larger volumes of material. Inclined screens help maintain organised material flow, supporting accessible routes and optimising material separation.
Mobile Screens
Mobile screens are portable vibrating screens designed for on-the-go deployment. Easily relocated across different areas of the mining site, these screens are ideal for creating temporary access routes and managing material flow wherever needed. Their flexibility allows for real-time adjustments to meet changing site demands.
Portable Screens
Portable screens are compact, adaptable vibrating screens designed for quick setup and efficient material classification. Their ease of deployment and versatility in handling various materials contribute to efficient material flow, enabling structured and accessible routes that adapt to the operational needs of the mining site.
Mills
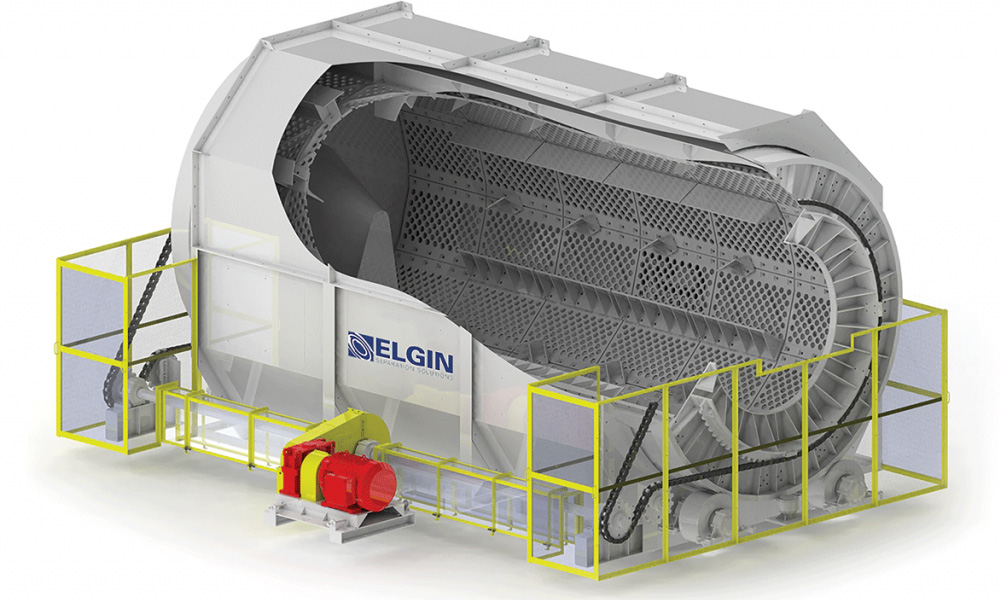
Mills are used to grind materials into finer particles, preparing them for subsequent processing or extraction stages. Different types of mills serve varying purposes based on the material’s hardness, size, and intended final product.
- Hammer Mills: Hammer mills use high-speed rotating hammers to crush and pulverize materials. Ideal for brittle and medium-hard materials, these mills are commonly used in mining to reduce materials to finer particle sizes.
- Ball Mills, Pebble Mills, Autogenous Mills, and Semi-Autogenous (SAG) Mills:
- Ball Mills: Ball mills use steel or ceramic balls as grinding media to reduce materials to fine powders, suitable for mineral dressing and other applications.
- Pebble Mills: Similar to ball mills, pebble mills use natural stones or ceramic as grinding media, offering a softer grinding action.
- Autogenous Mills: These mills rely on the material itself as the grinding medium, ideal for coarse grinding and primary milling.
- Semi-Autogenous (SAG) Mills: SAG mills combine a small amount of grinding media with the material itself for the grinding process, offering high-capacity milling and often used in primary grinding stages.
- Mill Liners and Feed Chutes: Mill liners are protective coverings inside mills that reduce wear on the mill’s interior and enhance grinding efficiency. Feed chutes direct materials into mills safely and efficiently, ensuring consistent input and reducing spillage. Both components contribute to the longevity and optimal performance of milling equipment.
Bunkers, Silos, Reclaimers
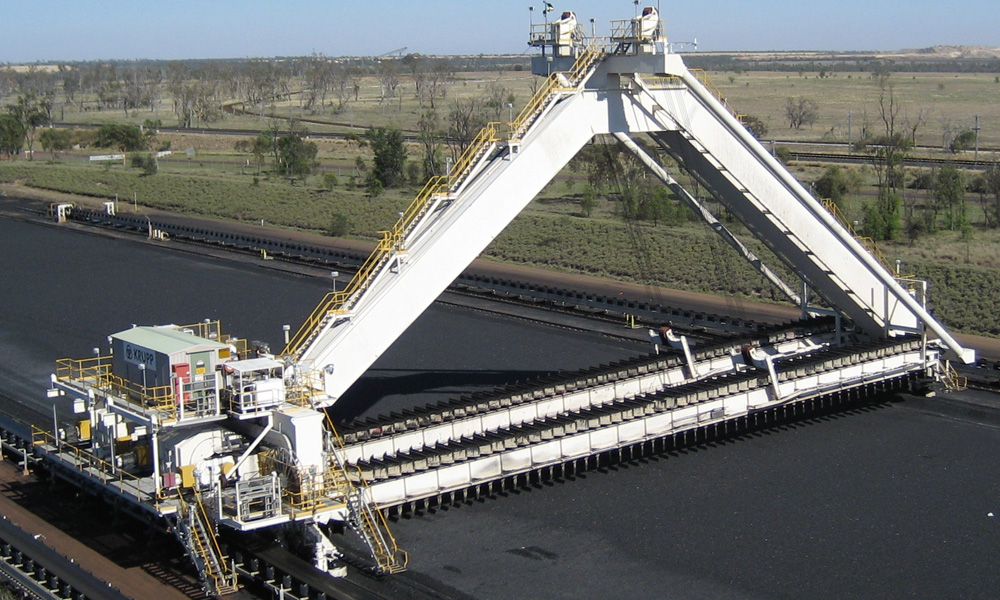
Bunkers, silos, and reclaimers are essential components in material storage and handling within mining operations. They provide structured, accessible storage solutions and facilitate the smooth retrieval and movement of materials across the site.
Bunkers
Bunkers are large storage structures designed to hold bulk materials temporarily, typically positioned near processing areas to provide easy access to necessary materials. They play a crucial role in ensuring that a steady supply of materials is available for processing and are often used for short-term storage to support continuous mining operations.
Silos
Silos are tall, cylindrical structures used for the long-term storage of bulk materials. They provide efficient storage solutions that protect materials from external conditions and ensure a controlled supply flow. By maintaining materials in an organized, accessible manner, silos help streamline the handling and processing stages within the mining site.
Portal Scraper Reclaimer
Portal scraper reclaimers are specialized machines designed to extract and retrieve materials from stockpiles, such as those within bunkers or silos. These reclaimers operate by scraping materials from the storage area and moving them onto conveyor belts or into trucks for transport. Their role in efficient material management helps maintain a continuous flow of resources, ensuring easy access to stockpiled materials and supporting the structured movement of materials across the mining site.
Shipping & Refining
After extraction and initial processing, mined materials embark on the next crucial phases: shipping and refining. Together, these steps ensure that raw materials are efficiently transported to refineries and processing facilities where they can be transformed into valuable end products.
Shipping in mining involves a range of logistics solutions designed to transport materials from the mining site to processing facilities. Whether through rail, road, or sea transport, efficient shipping strategies help minimise costs, reduce carbon footprint, and ensure timely delivery. Advanced bulk carriers, specialised containers, and even eco-friendly rail systems are now part of modern shipping solutions, reflecting the industry’s commitment to both productivity and environmental responsibility.
Refining is where raw mined materials are processed to remove impurities and enhance their quality for specific uses. This process varies depending on the material type—metals like copper or gold undergo smelting and electrolysis, while minerals might be refined using flotation or leaching techniques. Refining increases the purity and value of the material, preparing it for industrial applications or consumer products.
Together, shipping and refining mark the final stages in the material’s journey from raw resource to refined product, setting the stage for use in manufacturing, construction, technology, and more.