Maintaining a C-17A Globemaster III is no small task. These aircraft are enormous, complex, and absolutely essential to military logistics operations. Keeping them in peak condition means maintaining their engines efficiently and safely—something that, until recently, was more cumbersome than it needed to be.
At RAAF Base Amberley, the process for servicing C-17A engines had long involved a maintenance stand system that was known to be outdated. It required four separate jacks, multiple operators, and a fair amount of time just to set things up. Adjustments were slow and repetitive and left plenty of room for inefficiencies and user error. So, Defence Australia and Boeing Defence Australia, working with SafeSmart, set out to modernise the system—making it safer, easier, and more effective.
Identifying the Problem
The primary challenge was clear: engine maintenance was taking longer than it should. The old stands supplied by the aircraft manufacturer weren’t just inefficient; they also introduced safety concerns, requiring careful manoeuvring and multiple hands on deck to position the behemoth. Not exactly a model of efficiency.
A new stand was needed that could fulfil all the tasks the old one was capable of, including:
- Work for both inboard and outboard engines
- Be adaptable to accommodate ladders and smaller platforms
- Meet strict safety regulations.
This wasn’t just about making life easier for maintenance crews—it was about ensuring safety, compliance, and operational efficiency. The goal was clear: make something that was faster, safer, and didn’t require an entire committee just to set up.
From Lumbering Behemoth to Nimble Giant

The new C-17A maintenance stand ditched the manual jack setup and introduced electronic actuators across the board.
With a simple push of a button, a single operator could adjust the height. No more endless cranking, no more synchronising four different jacks. Just press, adjust, and get on with the job. But that wasn’t the only bit of innovative engineering:
- Removable Rear Frames & Self-Levelling Stairs – The rear frame could be detached so the whole stand could be towed into place without getting in the way of the engine. Meanwhile, self-levelling stairs ensured mechanics didn’t have to do an awkward balancing act while carrying tools.
- Safety, But Smarter – Anti-static reels, checker plate decking with an epoxy coating (normally used in marine applications like ship walkways) for grip in greasy and wet conditions, and telescopic guardrails that are easily configurable for the task at hand, kept workers secure without obstructing access.
Everything was designed with the people using it in mind.
Looks Good, Works Better
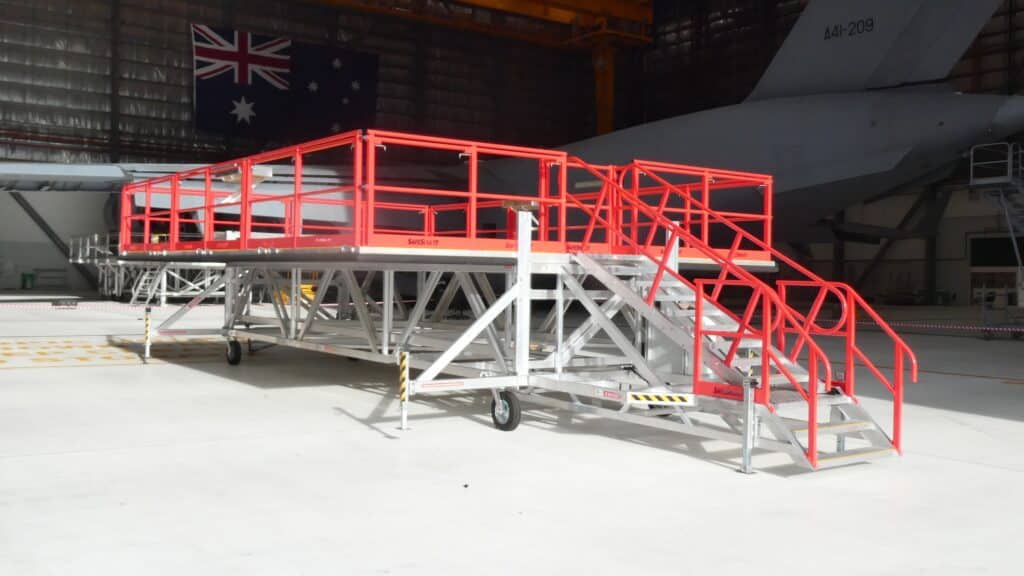
The design was meticulously simulated, stress-tested, and scrutinised to from engineers internal and external. The stand was not only up to the AS1657:2018 standard, but it was also designed to be disassembled and transported inside a C-17A itself. That meant it could be used wherever the aircraft was deployed—a rather handy feature for global operations.
And the best part? Less maintenance downtime, fewer people required for setup, and improved safety meant fewer delays, reduced costs, and happier engineers.
Next to come was building the platform.
The Moment of Truth
For other companies, the delivery phase is where everything falls apart—literally, in some cases. But not here.
With every single part and every single feature meticulously designed by in-house engineers with consultation from RAAF Base Amberley, production flew past at haste. And delivery was just around the corner:
- Pre-assembled units were sent straight to Amberley, ready to go.
- Comprehensive manuals were provided.
- On-site assembly support, managed by SafeSmart Access, ensured everything was set up correctly.
- Test-fits, training and induction on use of the stands completed the handover.
Hangar teams were ecstatic to have their new platform set up and ready to aid them in their C-17A maintenance tasks. A more-than-significant improvement over the time spent setting up, manoeuvring, and safety concerns of the old OEM platform.
It was a night-and-day improvement for crews on the ground, and they were keen to see the platform well used through its lifetime of service.
Keeping It Running
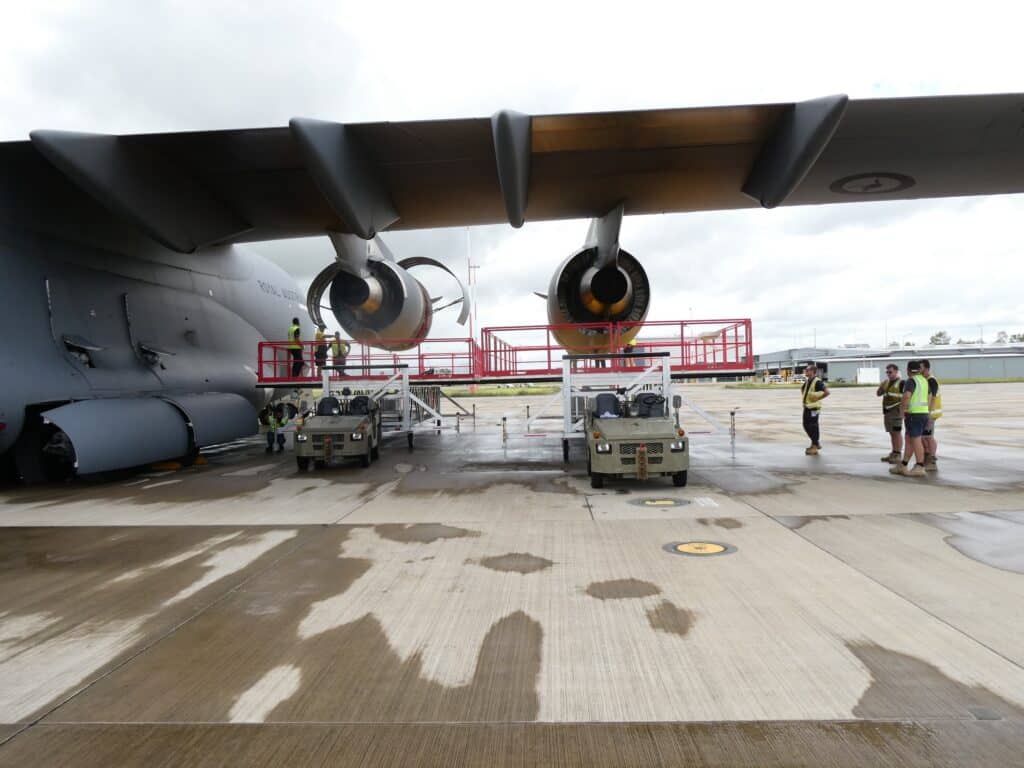
Once these new stands were in use, the SafeSmart Access team didn’t just walk away and hope for the best. Instead, through-life support was built into the offering:
- Spare parts are available for manufacturing, so maintenance crews aren’t left waiting six months for a replacement.
- Battery testing was run over 15 full cycles during the test, only reducing the battery charge from 100% to 99.4%.
- Training and documentation were updated.
- Feedback loops meant the design could be tweaked and improved over time, ensuring that this wasn’t just a one-off success but an ongoing evolution of smarter maintenance.
A Maintenance Win
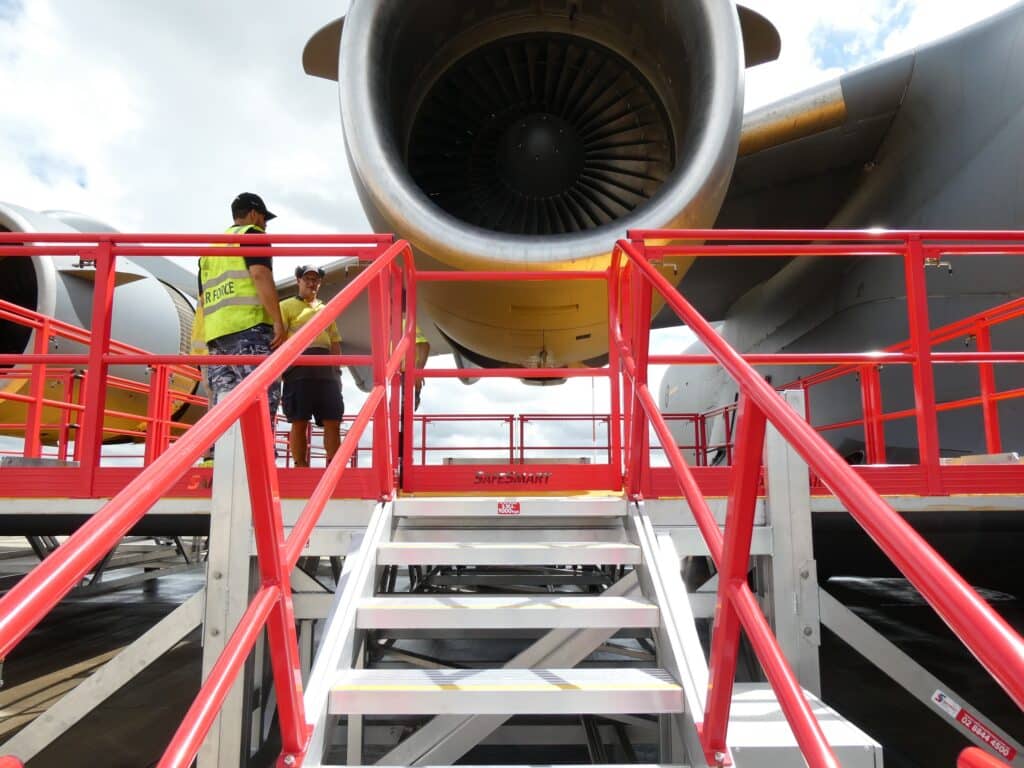
A maintenance stand that makes C-17A engine work faster, safer, and considerably less annoying.
Defence Australia and Boeing Defence Australia, with SafeSmart’s engineering prowess, have transformed what was once an awkward, multi-person job into a streamlined, one-operator process. They’ve reduced risks, reduced inefficiencies, and made life easier for the people keeping these giants in the air.
And the best part? This isn’t just about one project—it’s a template for how military aviation maintenance should be done. No wastage, no unnecessary complexity, just clever engineering solving real-world problems.
Why OEM Maintenance Stands Don’t Always Stand Up to Scrutiny
It’s perfectly logical to trust aircraft manufacturers to build high-performance aircraft—they are experts in aeronautical engineering, after all. However, designing a maintenance stand calls for an entirely different skill set.
Simply put, the expertise required for building a world-class airplane isn’t the same as the expertise required for crafting user-focused, safety-compliant work platforms.
By automatically relying on OEM stands, you may be settling for a solution that isn’t fully optimised for your day-to-day maintenance needs. Aircraft manufacturers’ primary goal is to produce exceptional airplanes; maintenance stands can sometimes be an afterthought.
On the other hand, companies that specialise in access and platform solutions focus exclusively on ergonomics, safety, regulatory compliance, and ease of use—all critical factors in a maintenance environment.
When your personnel are standing on these platforms, shouldn’t you rely on the specialists for work-at-height safety? If you wouldn’t trust a platform manufacturer to build your next military aircraft, it’s worth asking whether you should automatically trust an aircraft manufacturer to design your maintenance stands.
If you’re unsure whether your current stands truly meet your operational and safety requirements, book a hangar safety audit or download our eBook, “The Secret to Aircraft Maintenance,” for insights into how specialised platforms can transform your maintenance processes.